Solid State 3D LiDAR

Innovative electronic design for AV and ADAS applications
The Challenge
Design the electronics of an automotive-grade LiDAR reference solution
CLIENT: Leddartech
.
LOCATION: Quebec City, QC, Canada
LeddarTech, a leading provider of LiDAR technology for the automotive industry, needed a partner to help them design the electronics of a solid-state 3D LiDAR solution for autonomous vehicles and ADAS applications. They faced a tight schedule and needed a solution with a small footprint while maintaining long-range performance, with stringent packaging and power consumption constraints. Additionally, multiple new components, including ASIC, optics, and SoC, were being developed simultaneously with the electronics.
Hardware and mechanical design concept and architecture
Power supply design meeting EMC requirements
Multiple new components developed simultaneously
Frantz Saintellemy, President & COO
Founded in 2007, LeddarTech is a leader in optical detection and ranging technology at the forefront of the most exciting innovations in advanced sensing today.

The Solution
A partnership with Orthogone to get electronic engineering expertise for a solid-state 3D LiDAR
Orthogone’s team of experts designed the electronics for a solid-state 3D LiDAR solution, using advanced technologies and innovative design methods to meet the client’s requirements. Our team came up with an extremely compact electronic design while using low-cost PCB technologies. By using mixed-signal, high-performance receiver chains with very low noise and high-dynamic range, we were able to provide more accurate and longer-range detection. The highly efficient multi-channel laser pulse driver circuits enabled lower power consumption and better heat dissipation.
ORTHOGONE'S SOLUTION WAS DESIGNED TO MEET THE AUTOMOTIVE INDUSTRY'S DEMAND
Orthogone also developed a custom ASIC, which improved performance and reduced the overall solution’s size. The team worked closely with the client’s optics and SoC teams to ensure seamless integration of all components.
HARDWARE DESIGN
Electronic design of multiple (4) high-speed digital and analog printed circuit boards (PCB), including:
- Hardware and mechanical design concept and architecture
- Power supply design meeting EMC and voltage transient requirements of automotive applications (ISO 16750-2, 7637-2)
- Hardware design of a high-density CPU sub-system based on Renesas V3M System on a Chip (SoC)
- Hardware design of a multi-channel high-power laser driver circuit
- Hardware design of an ultra-low noise multi-channel receiver detector circuit based on a photodiode array and mixed-signal LiDAR ASSP (LeddarTech – LCA2)
- SPICE Simulations of analog sub-circuits listed above
- Post-layout simulations of high-speed mixed-signal circuits
- Functional bring-up, tests and integration to deliver a successful product launch at CES 2018
TECHNOLOGY
- LeddarTech LCA2 LiDAR ASIC
- Renevas V3M SoC
- Multi-channel laser die (wire bonding)
- Multi-channel photodiode array
The Result
A Cutting-Edge Solid-State 3D LiDAR Solutions
The solution was compact, efficient, and provided long-range performance, making it ideal for use in the automotive industry for autonomous vehicles and ADAS applications. The project was completed ahead of schedule, and the client was able to bring their product to market quickly, thanks to Orthogone’s expertise and dedication to meeting their needs. LeddarTech had a successful product introduction at CES 2018 and won the prestigious Innovation 2018 Award in two categories.
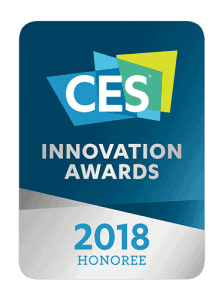
LeddarTech successfully showcased its products at CES 2018 and won the prestigious 2018 Innovation Award in two categories.